China Cheap price Finishing Auxiliaries - 44196 Fixing Agent (For improving wet rubbing color fastness) – Innovative
China Cheap price Finishing Auxiliaries - 44196 Fixing Agent (For improving wet rubbing color fastness) – Innovative Detail:
Features & Benefits
- Contains no APEO or formaldehyde. Fits environmental protection requirements. Comply with requirements of European Union OEKo-TEX Standard 100.
- Greatly improves1~1.5 grades of wet rubbing color fastness and makes it up to more than 3 grades.
- Imparts fabrics soft hand feeling.
- Not influences color shade or light fastness.
- Saves time and energy. Cost-effective.
Typical Properties
Appearance: | Light yellow to yellow transparent liquid |
Ionicity: | Weak cationic |
pH value: | 4.5±1.0 (1% aqueous solution) |
Solubility: | Soluble in water |
Content: | 40% |
Application: | Cotton and cotton blends |
Package
120kg plastic barrel, IBC tank & customized package available for selection
TIPS:
Continuous dyeing
Continuous dyeing is a process whereby dyeing the fabric and fixation of the dye are carried out continuously in one simultaneous operation. This is traditionally accomplished using a production line system where units are assembled into lines of consecutive processing steps; this can include both pre- and post-dyeing treatments. Fabric is usually processed in open width, so care must be taken not to stretch the fabric. The fabric running speed dictates the dwell time of the fabric through each treatment unit, although dwell times can be increased by using ‘festoon’ type fabric transport. The main disadvantage to continuous processing is that any machinery breakdown can cause ruined fabric due to excessive dwell times in specific units whilst the breakdown is being rectified; this can be a particular problem when stenters running at high temperatures are employed since fabrics may be severely discolored or burnt.
The application of dye can be conducted either by direct application, whereby the dye liquor is sprayed or printed onto the substrate, or by continuous immersion of the fabric in a dyebath and excess dye liquor removed by squeeze rollers (padding).
Padding involves passing the substrate through a pad trough containing the dye liquor. It is imperative that the substrate is wet out thoroughly as it passes into the dye liquor to minimize unlevelness. The amount of dye liquor retained by the substrate after squeezing is governed by the pressure of the squeeze rollers and substrate construction. The amount of liquor retained is termed “pick up”, a low pick up being preferable since this minimizes migration of dye liquor in the substrate and saves energy during drying.
In order to obtain a uniform fixation of dyes on the substrate, it is preferable to dry the fabric after padding and before it passes on to the next process. Drying equipment is normally infrared heat or by hot air stream and should be contact-free to avoid marking of the substrate and soiling of the drying equipment.
After drying, the dye is only deposited on the surface of the substrate; it must penetrate into the substrate during the fixation step and become part of the substrate via chemical reaction (reactive dyes), aggregation (vat and sulphur dyes), ionic interaction (acid and basic dyes) or solid solution (disperse dyes). Fixation is performed under a number of conditions depending upon the dye and substrate involved. Generally saturated steam at 100°C is used for the majority of dyes. Disperse dyes are fixed in polyester substrates by the Thermasol Process whereby the substrate is heated to at 210°C for 30–60 s in order for the dyes to diffuse into the substrate. After fixation substrates are usually washed to remove unfixed dye and auxiliaries.
Product detail pictures:
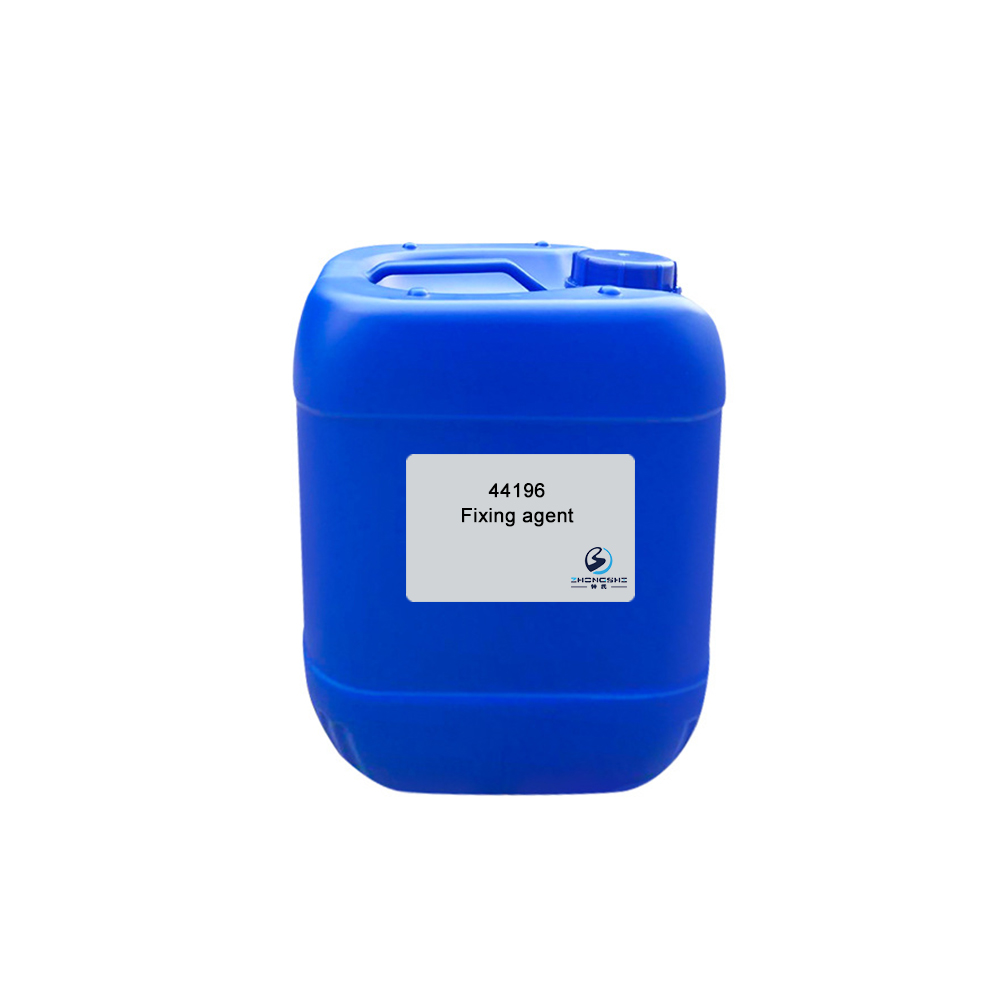
Related Product Guide:
Dispersing agent can improve luster and leveling effect. It can prevent floating, improve tinting strength, decrease viscosity, reduce flocculation, increase storage stability, increase color spreading property and increase color saturation. China Cheap price Finishing Auxiliaries - 44196 Fixing Agent (For improving wet rubbing color fastness) – Innovative , The product will supply to all over the world, such as: Puerto Rico, Munich, El Salvador, High Concentration Degreasing Agent 11045 appearance is Transparent liquid, ionicity is Nonionic, pH value is 7.0±1.0 (1% aqueous solution) and solubility is Soluble in water.

Hope that the company could stick to the enterprise spirit of "Quality, Efficiency, Innovation and Integrity", it will be better and better in the future.
