Manufacturer of Synthetic Fiber Wetting Agent - 43512 Anti-oxidation Agent – Innovative
Manufacturer of Synthetic Fiber Wetting Agent - 43512 Anti-oxidation Agent – Innovative Detail:
Features & Benefits
- Excellent property of resistance to high temperature oxidation and yellowing.
- Effectively prevents and reduces gas fading.
Typical Properties
Appearance: | Transparent liquid |
Ionicity: | Nonionic |
pH value: | 6.5±1.0 (1% aqueous solution) |
Solubility: | Soluble in water |
Content: | 20% |
Application: | Nylon, spandex and nylon/ spandex, etc. |
Package
120kg plastic barrel, IBC tank & customized package available for selection
TIPS:
Classification and properties of textile fibers
Despite the diversity of the physical and structural forms in which they come and chemical composition of the substances from which they are made the technology of producing all textile materials starts from the same initial point which is fibers. Textile fiber is defined as a textile raw material generally characterized by flexibility, fineness and high ratio of length to thickness. It is estimated that some 90% of all fibers are first spun into yarns, which are then converted into fabrics, and only about 7% of fibers are directly used for the manufacture of the end-use products. Processes used for the production of textile materials can be subdivided into four main groups as follows:
1. Production of fibers which can be natural or man-made.
2. Production of yarn where certain technical differences exist in spinning cotton, wool, synthetic fibers and fiber blends.
3. Manufacture of woven, knitted and nonwoven fabrics, carpets, webs and other sheet materials.
4. Fabric finishing which includes bleaching, dyeing, printing and special treatments aimed at giving the final product specific properties like water repellency and anti-bacterial and fiber-retardant properties.
Traditionally fibers are classified according to their origins. Thus fibers can be (i) natural, which in turn are subdivided into vegetable, animal and mineral and (ii) man-made, which are produced from natural or synthetic polymers, and others such as carbon, ceramic and metal fibers. This classification is continuously updated mainly due to the advances in the manufacture of man-made fibers.
The application of colorants, be they dyes or pigments, to textiles can be done at different stages on the route of converting fibers into the final product. Fibers can be dyed in the form of loose mass and then used in the manufacture of either solid shade or melange yarns. In this case particular care must be taken not to cause any damage to the fibers because this may create difficulties in spinning.
There are several possible scenarios for fiber dyeing as follows:
1. Dyeing a loose mass of single fiber, for example, 100% cotton or 100% wool. This may seem to be the simplest case but nevertheless the variation in fiber properties may cause variation in the resultant color between the batches.
2. Dyeing fiber mixtures of similar origins by the same type of dyes, for example, cellulose fiber mixtures or protein fiber mixtures. The difficulty here is to achieve the same color depth in all components. For this dyes must be specifically selected in order to equalise the differences in fiber dyeability.
3. Dyeing fiber mixtures of different origins where it is possible to obtain color effects by dyeing each component to a different color. In this case it is necessary to provide uniform fiber mixture before the dyeing; an additional re-mixing after dyeing may still be required.
4. Dyeing the natural and synthetic fiber blends where typical cases are cotton/polyester, wool/polyester, wool/acrylic and wool/polyamide blends.
The selection of fibers for these blends can be explained by the complementary properties of the components. These blends represent a considerable proportion of textiles used for apparel due to lower production cost, good comfort characteristics, improved durability and better dimensional stability in comparison to 100% natural and 100% synthetic fiber products.
Product detail pictures:
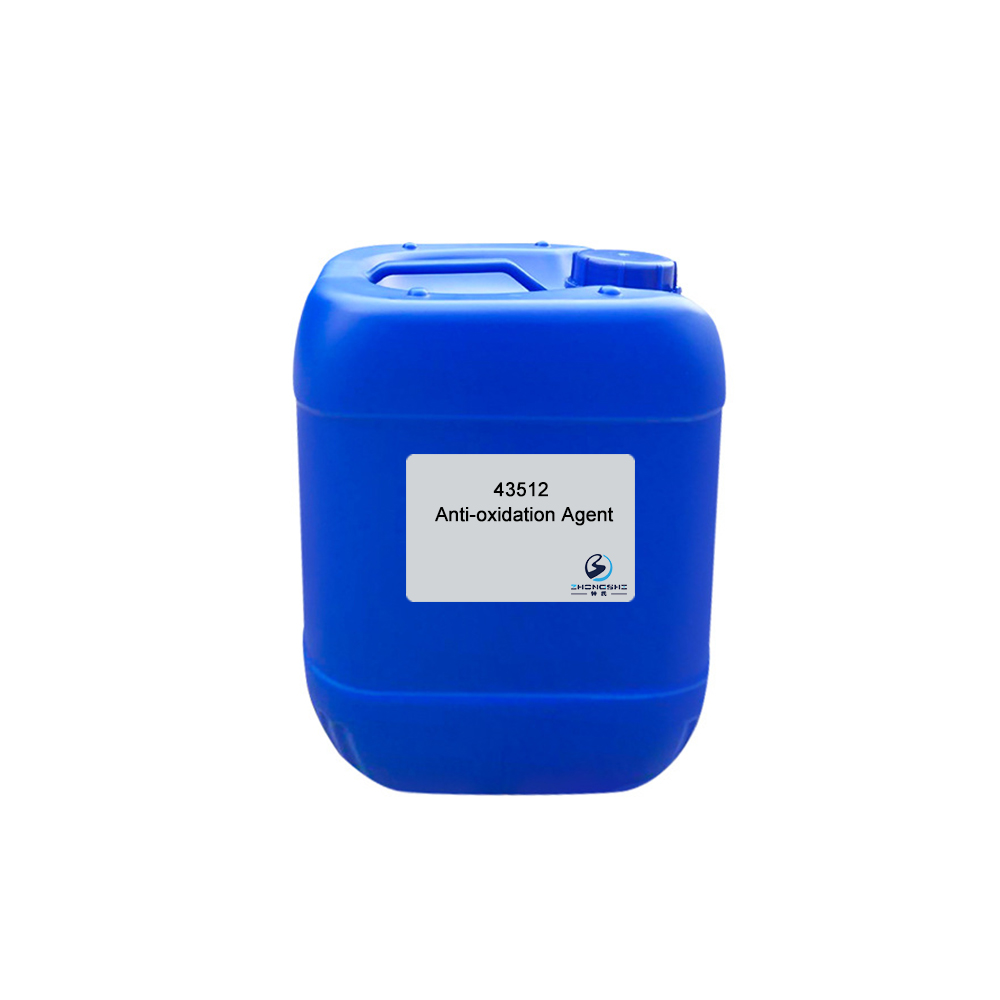
Related Product Guide:
Soaping agent is used to remove the unfixed dyes and hydrolytic dyes on fabrics and prevent color spots on fabrics, which improves the product quality. Manufacturer of Synthetic Fiber Wetting Agent - 43512 Anti-oxidation Agent – Innovative , The product will supply to all over the world, such as: Venezuela, Rwanda, Berlin, Fixing Agent 23014 is light yellow liquid. It is cationic dyeing auxiliary, which can be soluble in water. Fixing Agent 23014 is suitable for polyester/ cotton. It is eco-friendly. Fixing Agent 23014 has certain inhibiting effect for bright red, black and blue disperse dyes. It can decrease the influence on fastness after setting. It is cost-effective, which saves cost and time. It has good compatibility.

The manufacturer gave us a big discount under the premise of ensuring the quality of products, thank you very much, we will select this company again.
